Cleveland Manufacturing’s most recent customer, Romac Products, has introduced a new and unique way of plating to the location and team.
Romac Products is an industry-leader in custom injection molding and chrome plated plastic. They have an extensive catalogue of emblems and name plates throughout the automotive industry.
The unique nature of the parts and rack structuring has involved innovation on the part of the Cleveland team. The size and number of the parts means they cannot be racked in the same way as Cleveland’s other customers. So, the Cleveland team needed to get creative to develop a new process and station to accommodate.
Jerika Lopez, Team Leader, and Sonia Pacheco, Production Supervisor – Lead , are part of the team involved in developing the process for Romac.
“At the beginning it was challenging,” explained Jerika. “Now we’ve set up a flow and organized everything to better understand it, and we have everything under control. I like being able to build everything from scratch, that’s the fun part.”
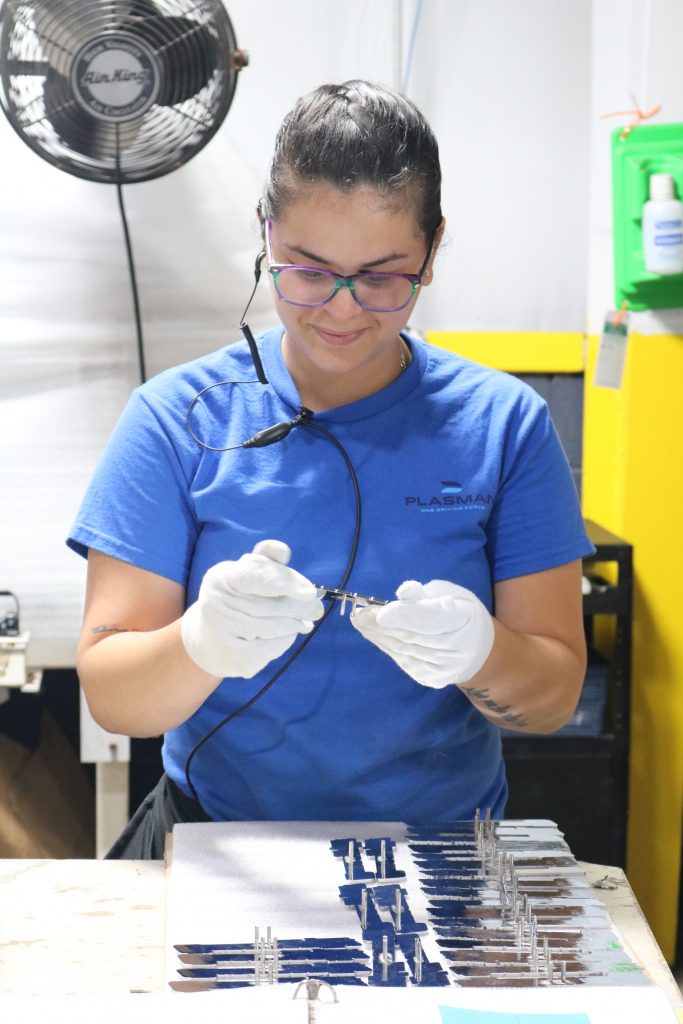
Jerika Lopez, Team Leader, analyzing Romac Products emblem after going
through the chrome line.
Typically, at Cleveland, IPNs (Individual Part Numbers) are assigned to each part that goes through the chrome line and that part takes up an entire rack. But, with Romac, the size of the parts means that anywhere from two to five different parts can fit on one rack. As well, given the various number of parts that can be sent to Cleveland, assigning IPNs to each part is not sustainable. Instead, they’ve assigned a IPN to each unique type of rack that is used for Romac.
“It is challenging and special at the same time, because every day is something different,” said Sonia. “We don’t know what emblems we are going to plate each day and it’s great to see the magic that the process team members create. There are different parts, different shapes, and we are getting to see it shine and make it happen which is just amazing.”
They have developed a board displaying each Romac emblem that can be seen at the new Romac station. The board not only helps visualize all the different parts, but also shows people who come to Cleveland the different things the plant is doing, explained Sonia.
Through teamwork and innovation, Cleveland has been able to bring in a unique plating partner.
“Plasman is built off of partnerships — partnering with suppliers, partnering with customers,” said Tim Aktas, General Manager, Cleveland Manufacturing. “And the whole point of building that partnership is to ensure mutual success between ourselves and our partners. It’s let’s do this together and let’s be successful together.”
Cleveland Manufacturing provides flexibility and possibility to their customers. With North America’s only hoist and return line under one roof, endless color selections, and custom applications, they are dedicated to making chroming visions a reality.
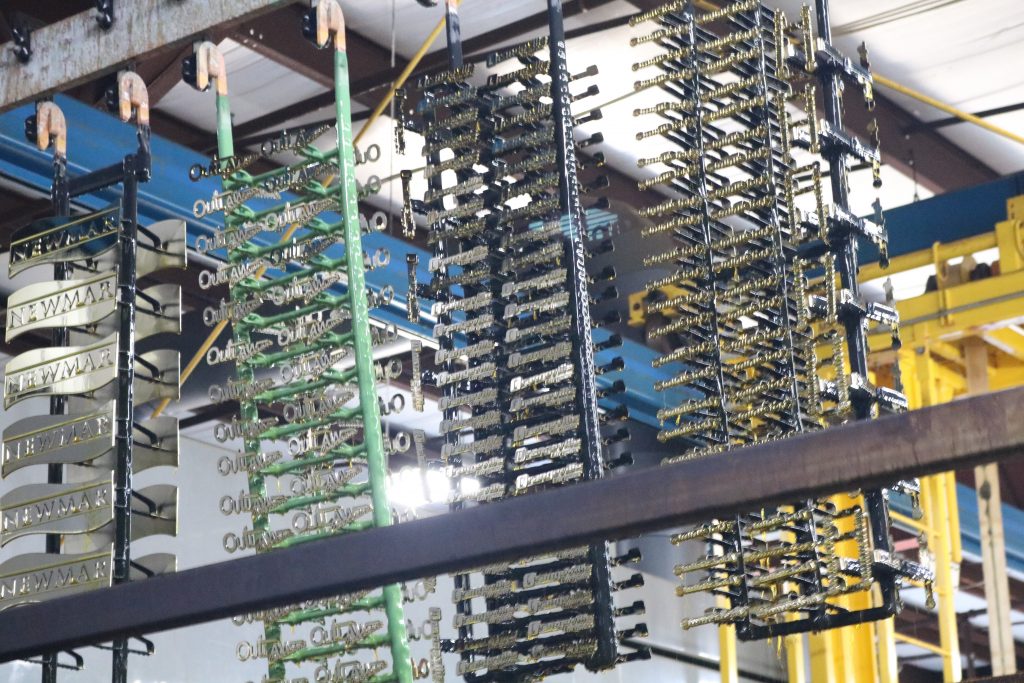
About Plasman
Plasman is a leading global manufacturer in bumpers-fascias, grilles, exterior trim, and subsystem components. As One Driving Force™, our diverse team of talented employees in 11 countries is driven by a commitment to outperform in all areas from engineering design to state-of-the-art manufacturing processes. Plasman’s headquarters are in Oldcastle, Ontario. Further information about Plasman is available at Plasman.com or follow us on LinkedIn.